Behind the scenes of the St Fagans live brief
- Jacqs Scourfield
- Dec 5, 2018
- 2 min read
Updated: Feb 6, 2021
Three weeks into the St Fagans live brief, my studio space is beginning to fill up with exciting new material samples. Integral to my project concept is the use of traditional materials found within museum collections. After becoming inspired by the picturesque mantelpiece scenes in the village cottages, I’ve carried out a material inquiry, challenging and recreating object forms and decorative details from traditional materials; metal, glass and china plates. Working with technicians within the university I utilised the university’s waterjet cutter, trialling, cutting, rusting steel, glass and old china plates. This was the first time I have explored cutting glass and ceramic, I was particularly intrigued by how intricate I was able to go with my artwork.

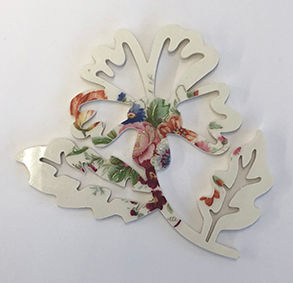
After exploring, mocking-up 3d forms in card, it was time to find some steel and trial cutting and creating the forms out of this desired materiality. The object concept was to transform a cut sheet of metal into a 3d form by folding and manipulating the metal into shape. Whilst I initially liked the weathered effect of the rusted steel, as a design brief, the project required sensitivity towards the use of a colour scheme. As a maker, the materiality I used naturally has been defining my colour palette; in response to this, I challenged myself to investigate new ways of adding colour to metal. Over the past week I have been working with a company from Pembrokeshire in order to get one of my metal mequettes powder coated. Part of the charm of my 3d forms is the precise cutwork, naturally the slick finish of the powder coated surface became the perfect combination to this. As we enter the final stages of the brief, I am excited to begin to produce a series of cut and powder coated metal forms, in a colour palette influenced by the architecture at the museum. I plan to create an installation of a mantelpiece scene featuring my metal components, alongside glass and ceramic pieces to create the narrative of patterns breaking free from the object forms.

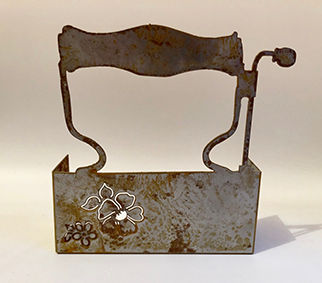
Water jet cut metal object, before and after powder coating
Working with powder coating specialists has enabled me to access new techniques, enhancing my professional development and practice. As a maker, proficiency in liaising with companies to oversee production of final products will be an asset to me, in both employed and self-employed roles, as I prepare to graduate from university and enter the big wide world later this year!
Comments